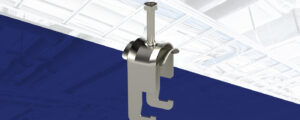
KS20 XPG® - sustainable cable ladder for atmospheric corrosion classes C1-C4
Cable ladder KS20 XPG®
The familiar KS20 cable ladder is now available with a new zinc-based special coating. The new KS20 XPG® cable ladder matches the dimensions and features of the versatile KS20 cable ladders, making the KS20 XPG® suitable for medium-heavy loads in building services and industrial applications, both indoors and outdoors, in atmospheric corrosion classes C1-C4. Installation parts for the KS20 and KS60 systems are compatible with the KS20 XPG® cable ladder.
Technical specifications and electrical numbers for the new products are:
SNRO | PRODUCT | WEIGHT (kg/pc) | A (mm) | S (mm) | L (mm) | PACKAGING |
---|---|---|---|---|---|---|
1433072 | KS20-200 L=3000 XPG | 5.72 | 200 | 1 | 3000 | 10 PCE / 30 MTR |
1433073 | KS20-300 L=3000 XPG | 6.2 | 300 | 1 | 3000 | 10 PCE / 30 MTR |
1433074 | KS20-400 L=3000 XPG | 6.72 | 400 | 1 | 3000 | 10 PCE / 30 MTR |
1433075 | KS20-500 L=3000 XPG | 6.89 | 500 | 1 | 3000 | 10 PCE / 30 MTR |
1433076 | KS20-600 L=3000 XPG | 7.98 | 600 | 1 | 3000 | 10 PCE / 30 MTR |
1433077 | KS20-200 L=6000 XPG | 11.25 | 200 | 1 | 6000 | 10 PCE / 60 MTR |
1433078 | KS20-300 L=6000 XPG | 12.13 | 300 | 1 | 6000 | 10 PCE / 60 MTR |
1433079 | KS20-400 L=6000 XPG | 13.08 | 400 | 1 | 6000 | 10 PCE / 60 MTR |
1433080 | KS20-500 L=6000 XPG | 13.78 | 500 | 1 | 6000 | 10 PCE / 60 MTR |
1433081 | KS20-600 L=6000 XPG | 15.42 | 600 | 1 | 6000 | 10 PCE / 60 MTR |
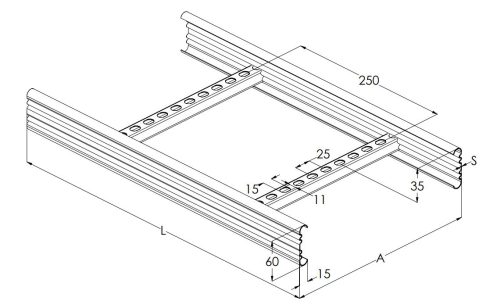
XPG® Coating
For several years now, we have been offering a new, certified, and extensively tested corrosion protection called XPG® alongside traditional hot-dip galvanized (HDG) products for C4 atmospheric corrosion class environments. The XPG® coating is a zinc-based metal alloy, with elements such as aluminum forming a thin film on the surface of the XPG® coating. This dense film enhances the corrosion protection properties of the coating compared to traditional zinc coatings. The corrosion protection of the XPG® coating is based on both cathodic protection and mechanical protection. XPG® provides similar corrosion protection in alkaline and acidic environments as other zinc-based coatings, while offering superior protection in chloride and ammonia-rich environments.
The manufacturers of the XPG® coating have thoroughly tested the coating. In addition to comprehensive tests conducted by the manufacturer, Meka has ensured that the XPG® coating meets high standards even when processed. Since spring 2018, we have been testing the new coating using various methods, such as continuous salt spray tests [ISO 9227, 550 h (equivalent to IEC 61537 class 6)], accelerated salt spray tests [VDA 621-415 (cyclic corrosion test)], penetrant inspection [SFS-EN ISO 3452-1], field tests in a real industrial environment, and bending tests at the University of Oulu.
The thin film that forms on the surface of the XPG® coating also protects areas of the product that are not coated, such as cut edges, welds, and scratches. However, under certain conditions, red rust may form on the uncoated surface of an XPG® product before the thin protective film can form. Over time, the film created by the XPG® coating covers any potential red rust, preventing steel corrosion. The speed at which the XPG® coating forms the film depends entirely on the environment. The more humid the environment, the faster the film forms.
The self-repairing protection process
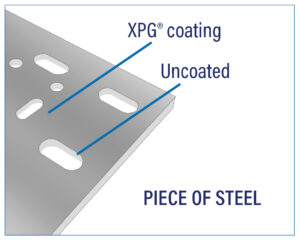
The thin film that forms on the surface of the XPG® coating also protects areas of the product that are not coated, such as cut edges, welds, and scratches.
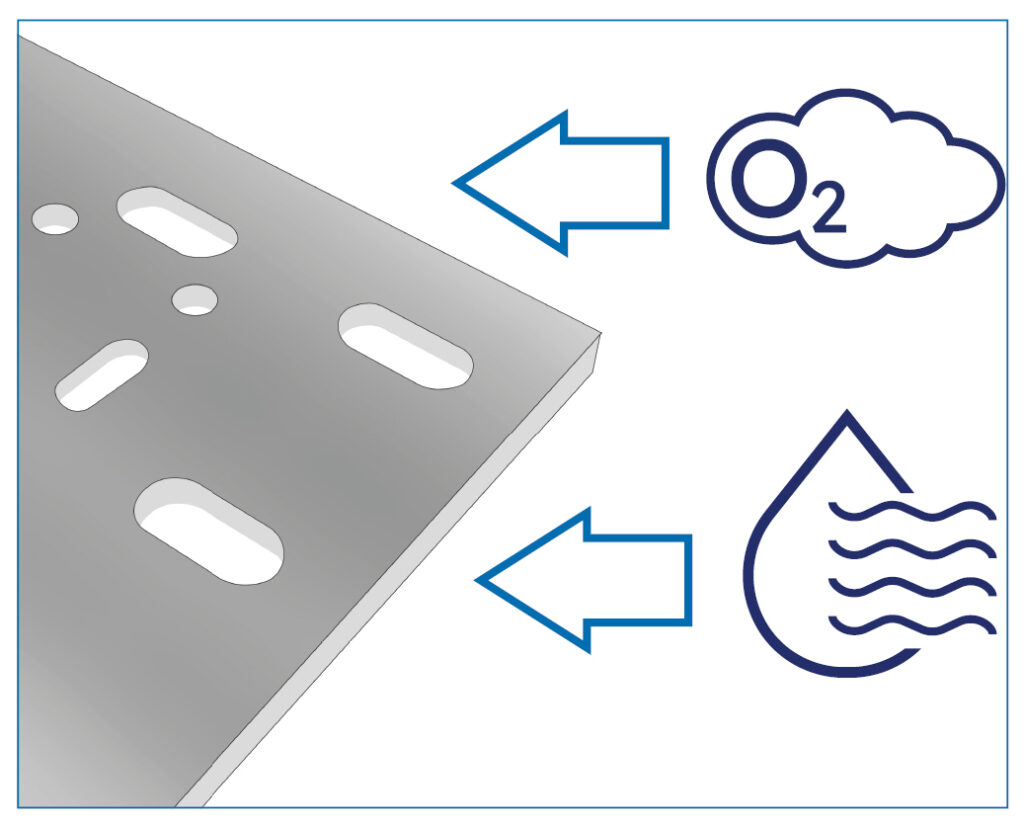
When the steel piece encounters oxygen and moist air, on the uncoated area may appear signs of slight corrosion.
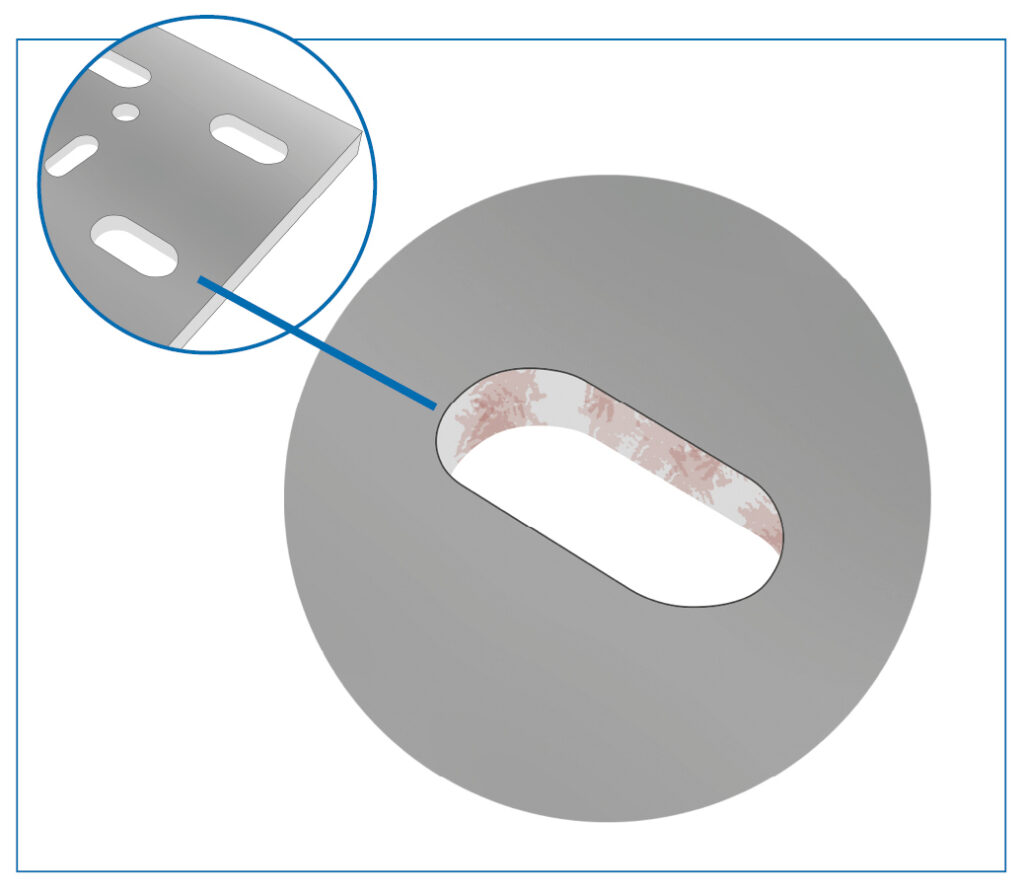
Mild corrosion (Red rust)
A thin film of XPG® coating components combined with ambient humidity gradually covers the unprotected surface.
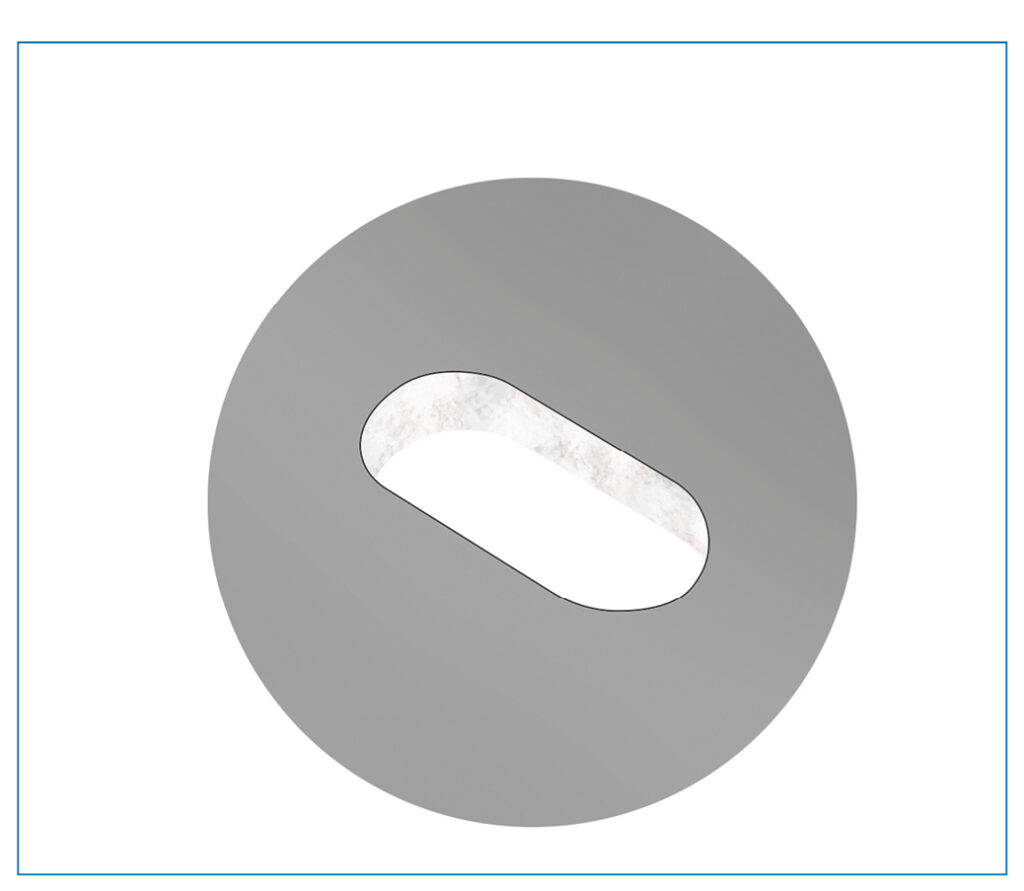
Protective layer
The white protective layer will soon completely cover the red rust. This protective layer completely seals the surface, preventing contact with the surrounding air and possible corrosion.
Features of the XPG® Coating:
- Clean and smooth finish on steel
- Cathodic and mechanical corrosion protection
- Enhanced corrosion protection with a thinner coating
- Self-healing coating
- More environmentally friendly option
- More cost-effective